At VOLTER, we offer a wide range of customisable options for our CNC routers, carefully tailored to meet each customer's unique production requirements. Our machines are designed to maximise functionality and efficiency, with enhancements such as increased gantry clearance for machining thicker materials, automatic tool changers to minimise downtime, and vacuum tables with adjustable zones for optimum material handling.
By working closely with our customers, we ensure that each CNC router is tailored to their specific requirements, with over 25 different options available to fine-tune performance and functionality. Whether it's adapting to the materials you work with or optimising your production process, we are committed to delivering a personalised solution that will enhance your manufacturing capabilities.
Options
Options by series
1. Basic configuration | PRO | L | ACP | SX |
---|---|---|---|---|
Solid welded steel frame | + | + | + | + |
Vacuum table of aluminium profiles | + | + | + | + |
Spindles 4.5 - 16 kW | + | + | + | + |
Touch-screen monitor | + | + | + | + |
Hand console | + | + | + | — |
Laser pointer | + | + | + | + |
Helical racks | + | + | + | — |
Brush foot | + | + | + | + |
Tool length sensor | + | + | + | + |
2. Options | PRO | L | ACP | SX |
---|---|---|---|---|
Automatic tool changer (7 tool positions) | + | + | — | + |
Automatic vacuum zone switching | + | + | + | — |
Pneumatic Locator Pins (PLP) System | + | + | + | + |
Phenolic vacuum table | + | + | + | + |
Tangential knife | + | + | — | — |
IP camera | + | + | — | + |
Tool lubricator | + | + | + | + |
Probe sensor | + | + | + | + |
Threading | + | + | — | + |
Extended Z axis clearance | + | + | + | — |
Safety light-beam sensors (2 sides) | + | + | + | + |
VECTRIC VCarve Pro software | + | + | + | + |
Vacuum pump BUSCH SAMOS 7,5 kW | + | + | + | + |
Vacuum pump BUSCH MINK 4 kW | + | + | + | + |
Dust collector MasterVac TS220 | + | + | + | + |
Dust collector MasterVac TS300 | + | + | + | + |
Pressure foot | + | + | + | + |
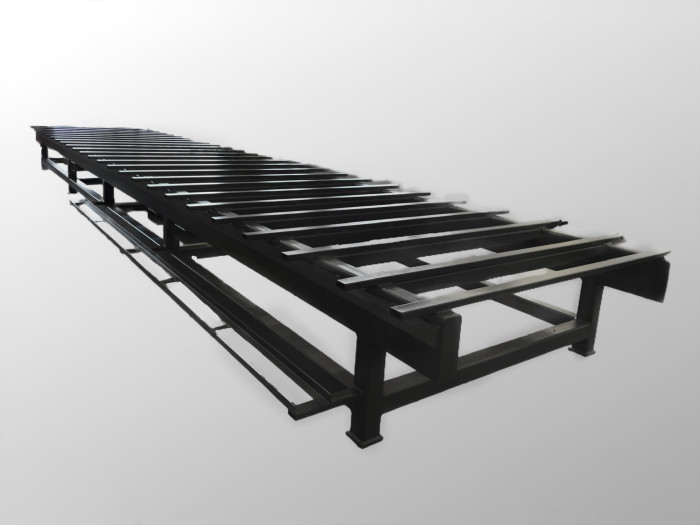
The steel frames of VOLTER CNC machines are meticulously crafted from welded cold-rolled steel pipes. Each frame undergoes thermal stabilization to ensure the preservation of its geometric integrity throughout the machine's lifetime. The mounting points for linear guides and helical racks are precisely machined using advanced high-precision machining centers, guaranteeing optimal alignment and performance.
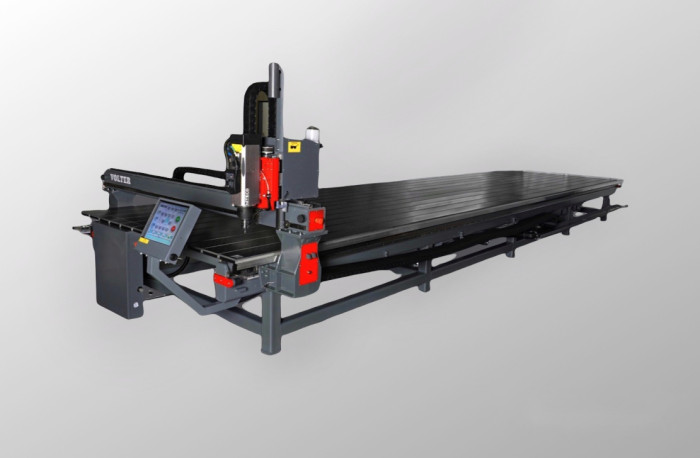
The vacuum hold-down is the most efficient solution for securely holding material in place on the machine during processing. The vacuum table is made of extruded aluminium profiles, covered with a sacrificial PVC layer and equipped with a system of vacuum valves to control the vacuum zones. The number of vacuum zones ranges from 4 to 12, depending on the size of the machine's processing area.
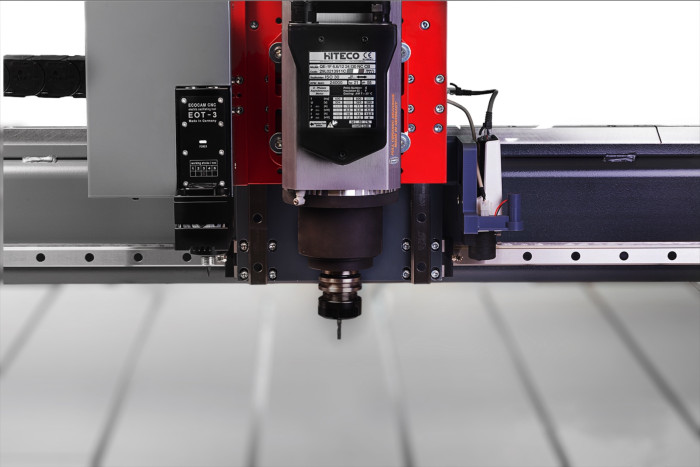
VOLTER CNC routers are equipped with high performance spindles from HITECO (Italy), offering air-cooled spindles from 4.5 to 10 kW and liquid-cooled spindles from 11 to 16 kW. All spindles use ER32 collets and customers can choose between pneumatic or mechanical clamping systems. The spindles deliver a maximum speed of 24,000 rpm, ensuring precise and efficient machining in a wide range of applications.
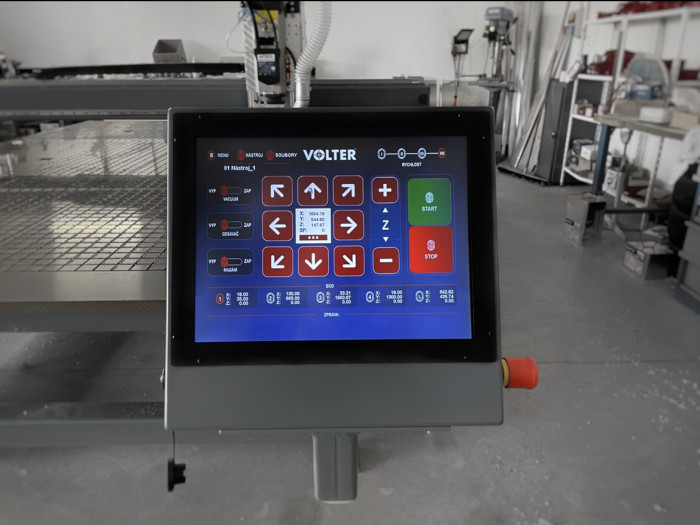
Touch-screen monitor is the main control panel of VOLTER CNC Routers. This monitor allows to control processing and change settings. User friendly interface has a modern, convenient and intuitive design.
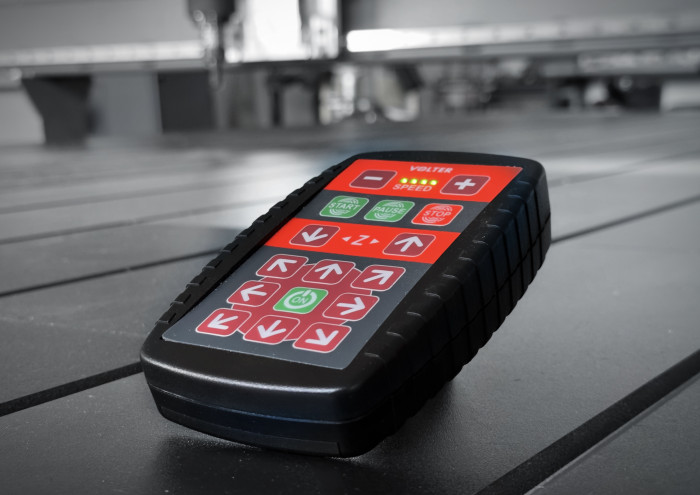
It is intended to move the cutting tool. It has an indication of the current speed of free movements and buttons to change this speed.
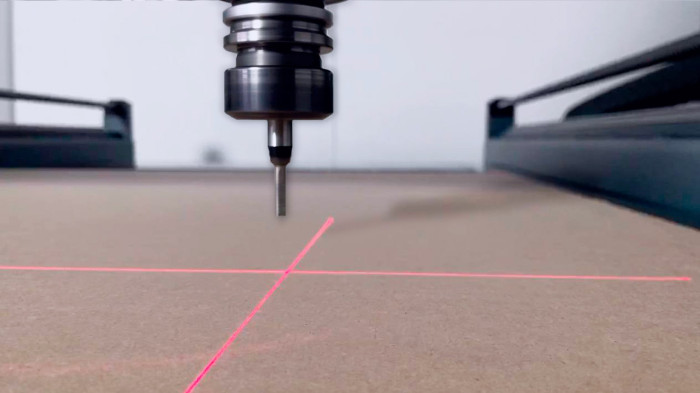
Laser pointer allows operator to set starting point of a job quickly and easily. It is enough for it to move the laser pointer to angle of sheet and click "Save" button on the touch screen monitor.
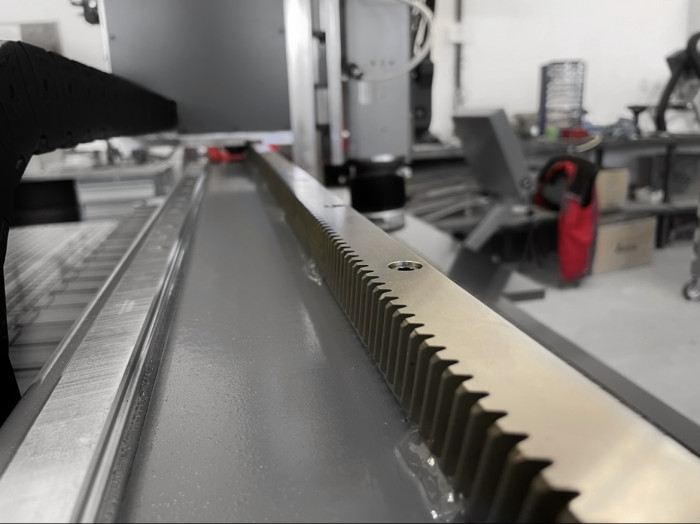
Helical racks set in X and Y axes. It increases the accuracy and quality of processing, reduce noise and vibrations during moving.
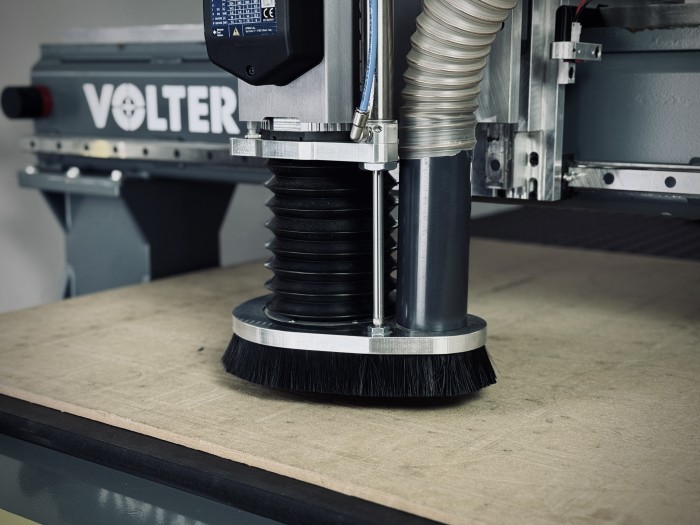
Designed to remove chips and waste from cutting zone.
Chips fall into a special chamber mounted on the spindle and are removed through a special pipe into the dust collector.
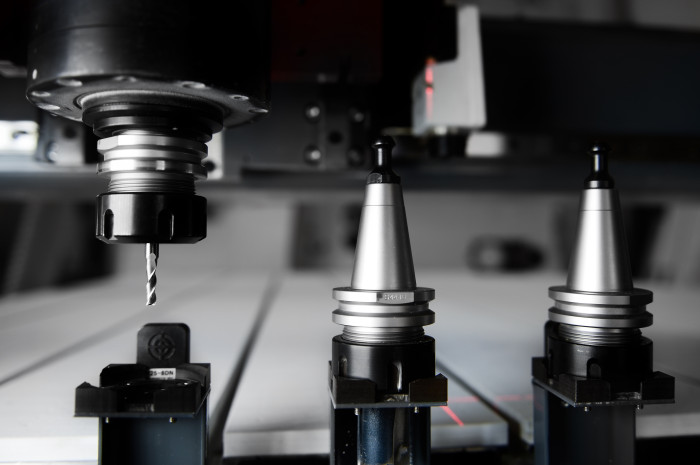
This system automatically changes tools during processing. It drastically saves time for jobs which need several tools for processing. Controller saves the length of each tool in the system. As a result, it is not necessary to measure tool length after changing a tool automatically. VOLTER automatic tool changer has 7 positions for tools. It is possible to add two ATC units.
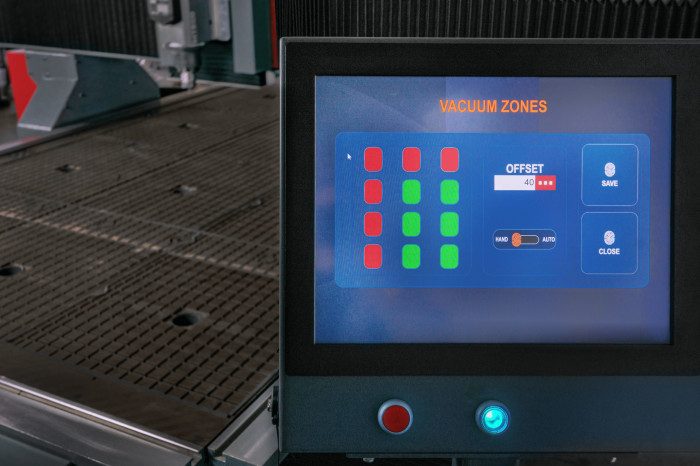
The Vacuum Hold-Down Zones Switcher optimizes material handling and increases production efficiency, enhancing the versatility and performance of VOLTER CNC Routers.
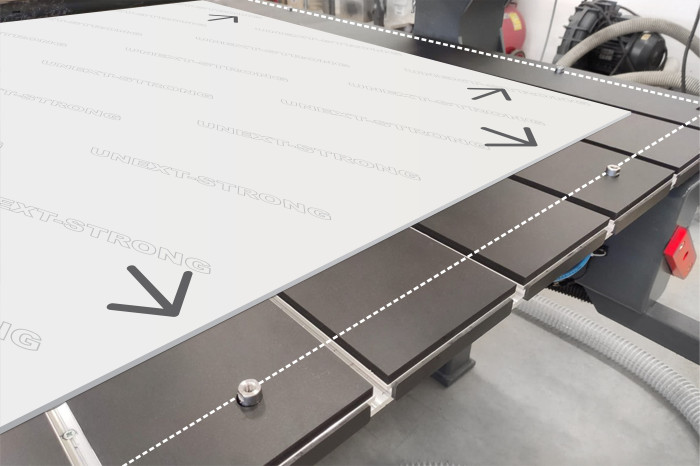
VOLTER Pneumatic Locator Pins lets to improve the performance of our machines for repeatable placement of cutting materials on table.
This system has 2 modes: hand and auto. In hand mode operator can raise and lower locator pins by button on touch screen monitor. In auto mode pins raise after finish of job and lower after start of new job.
Two rows of pneumatic cylinders make the material placement process faster and more precise.

The phenolic vacuum table provides a stronger vacuum pressure of the material on the surface. Almost perfectly flat working surface. Almost perfectly flat work surface. This solution allows quick replacement of the exposed layer on the working surface of the machine. It is an excellent choice for working with plastic, acrylic, composite and leather.
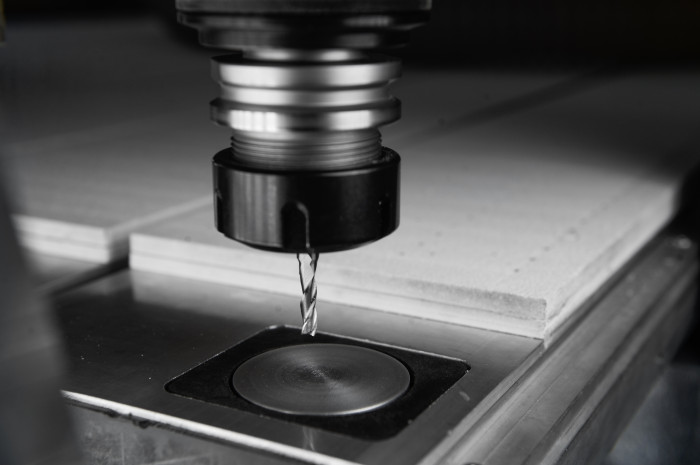
The sensor measures accurately and quickly the length of the tool. The operator need only press a button on the touch screen monitor, and this measurement will be performed.
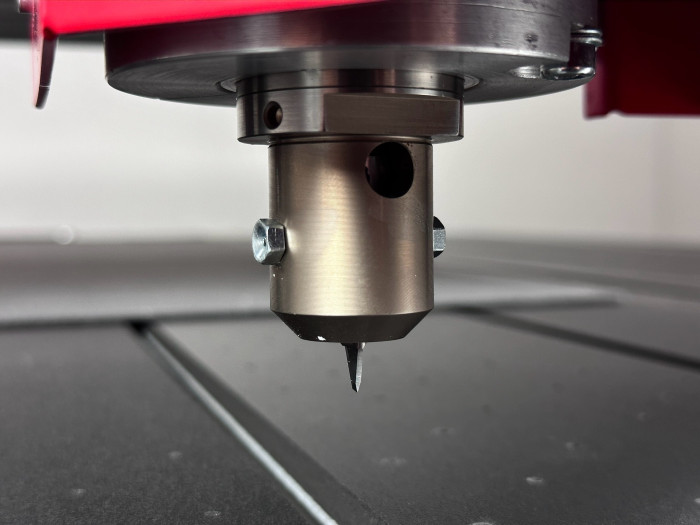
The blade automatically rotates in the direction of cutting. A Stepper motor is used to rotate the blade. It is possible to cut various materials: plastics, leather, fabrics, corrugated cardboard.
The oscillation mode of the blade allows to cut honeycomb materials, rubber and other soft packaging materia
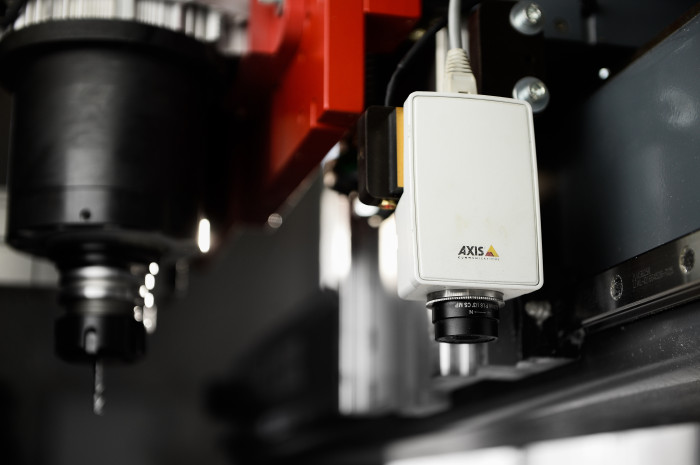
The option allows to cut the printed image along the contour. When preparing a file for printing, marks are added to the file — black circles with a diameter of 5-8 mm placed behind the contour of the image to be cut.
Printed image is placed on the machine and after starting the job, the camera checks locations of marks. Special software of the machine make adjustments to the job file. It lets to cut printed image exactly on the contour regardless of geometric distortions encountered in print and location of printed image on the machine.
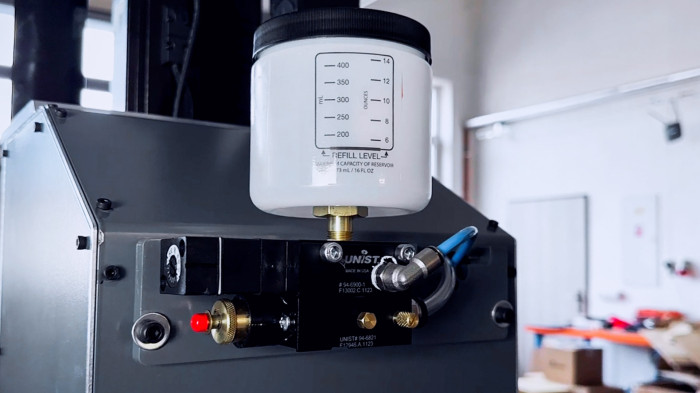
The system carries out a dosed supply to the cutting zone of lubricant emulsion or air flow. Continuous supply of lubricant (in the form of oil mist) or compressed air lets to maximize tool lifetime, improve quality of processing and increase speed of processing. It is necessary to connect an external pressed air supply with a working pressure of at least 6 bar to operate this lubrication system.
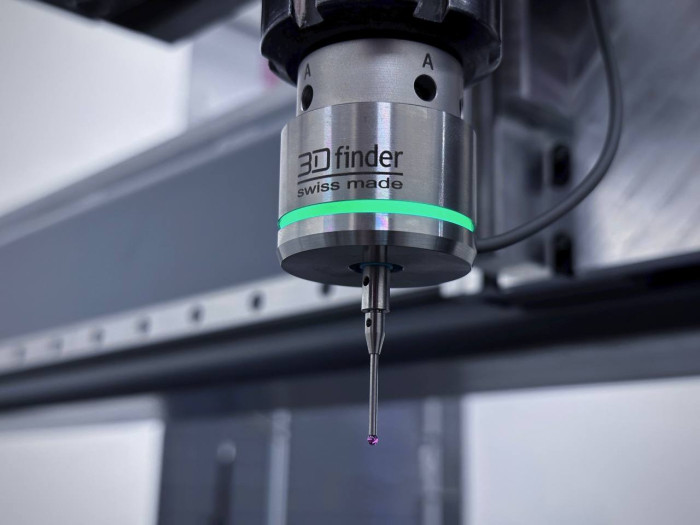
The Probe Sensor option enhances the capabilities of VOLTER CNC routers by automating material positioning, center hole finding, and surface height measurement. This improves the accuracy and efficiency of the processing.
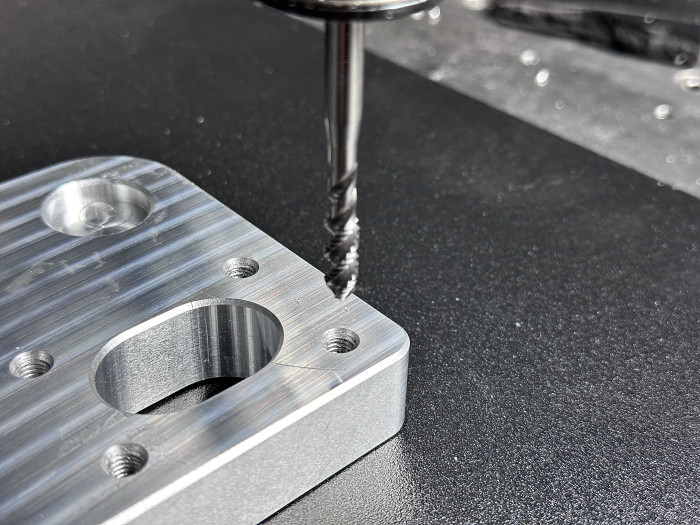
The VOLTER CNC threading option enhances the accuracy and speed of creating threads, reducing setup time and minimizing errors. This makes it ideal for applications requiring high precision, such as in the manufacturing of mechanical components and assemblies.
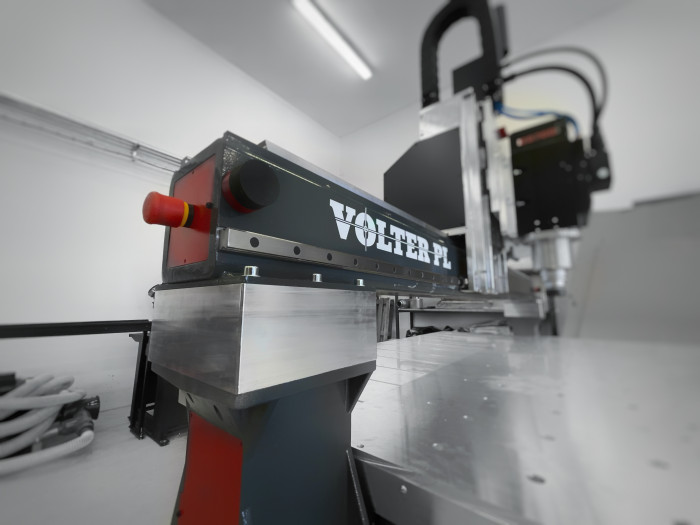
VOLTER L series machines have a portal clearance of 160 mm as standard, which allows processing materials with a thickness up to 150 mm. For processing thicker materials, we offer an option to increase the portal clearance up to 250 or 350 mm.
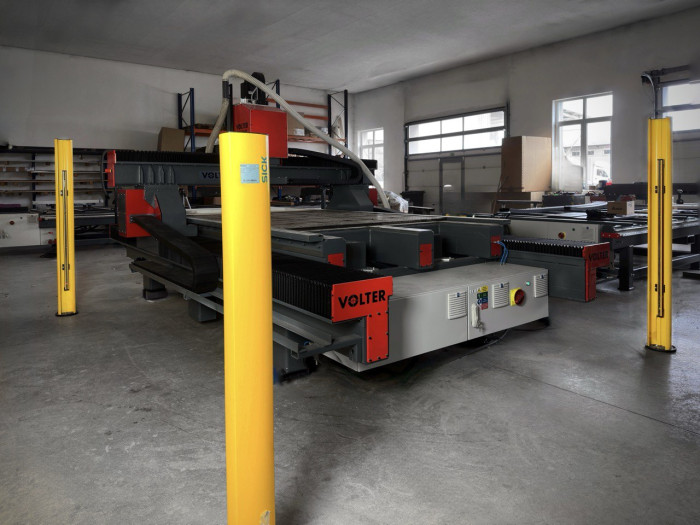
The Safety Light-Beam Sensors enhance the safety and usability of VOLTER CNC routers by providing an additional layer of protection for operators. Installed on both sides of the machine, these sensors detect any interruption in the light beam, immediately pausing the operation to prevent accidents and ensure a safe working environment.
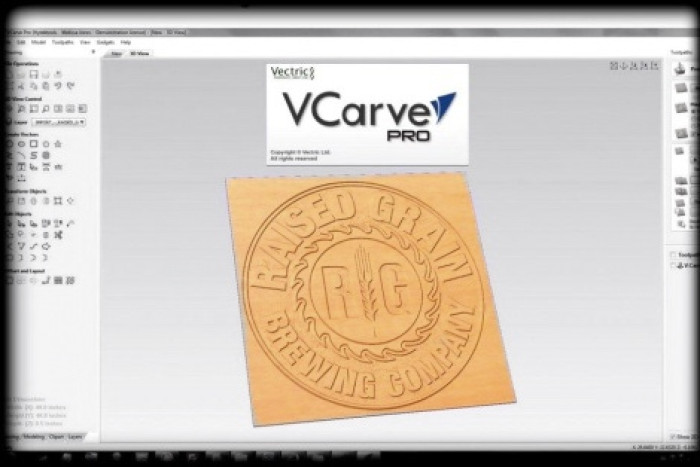
VECTRIC VCarve Pro software to create and prepare 2D and 3D files for CNC Routers. Large selection of formats for importing files, intuitive interface.
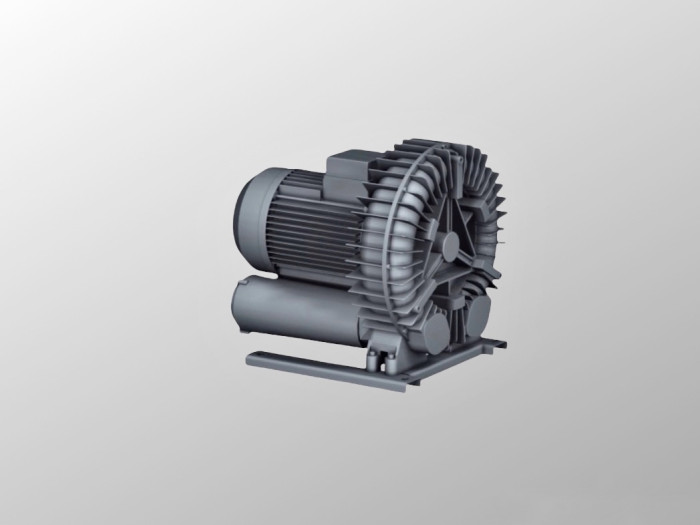
High efficient 7.5 kW vortex blower is supplied complete with air filter, pressure gauge, safety valve and fittings for connecting to the machine. Do not require maintenance during the entire life cycle.
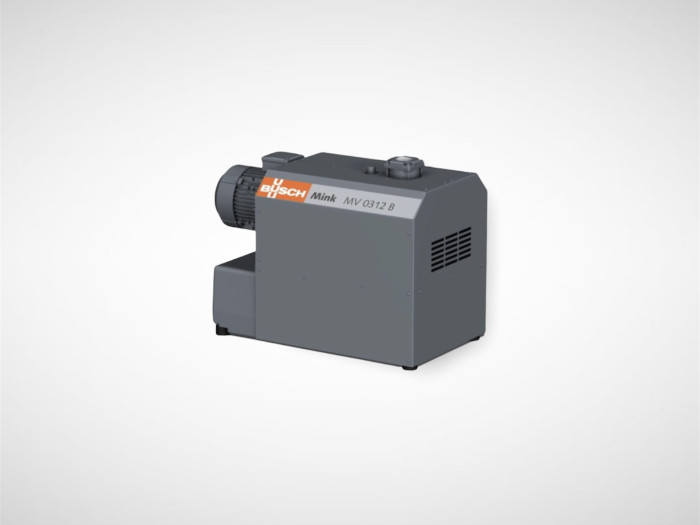
Rotary vacuum pumps Busch MINK (Germany) are an effective and reliable solution for vacuum hold down of materials. The cam rotors do not come into contact with each other or with the cylinder in which they rotate. The extremely small clearances between the cam rotors and the casing optimize the internal seal and guarantee a consistently high pumping speed without using of lubricating fluids.
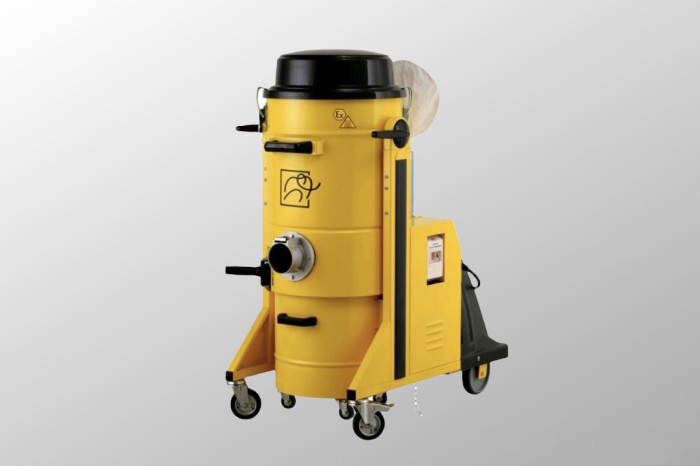
TS 220 is a reliable industrial dust collector for removing chips and dust during processing of various materials. The model is designed to work in the most hard operating conditions. Equipped with an industrial three-phase electric motor 400 V / 2200 W and a vacuum turbine with a side channel. The dust collector has a 30 l chip storage tank.
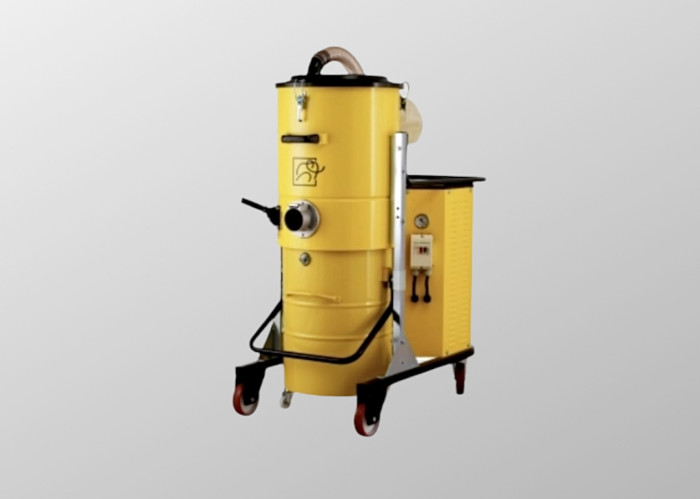
TS 300 is a reliable industrial dust collector for removing chips and dust during processing of various materials. The model is designed to work in the most hard operating conditions. Equipped with an industrial three-phase electric motor 400 V / 2200 W and a vacuum turbine with a side channel. The dust collector has a 100 l chip storage tank.
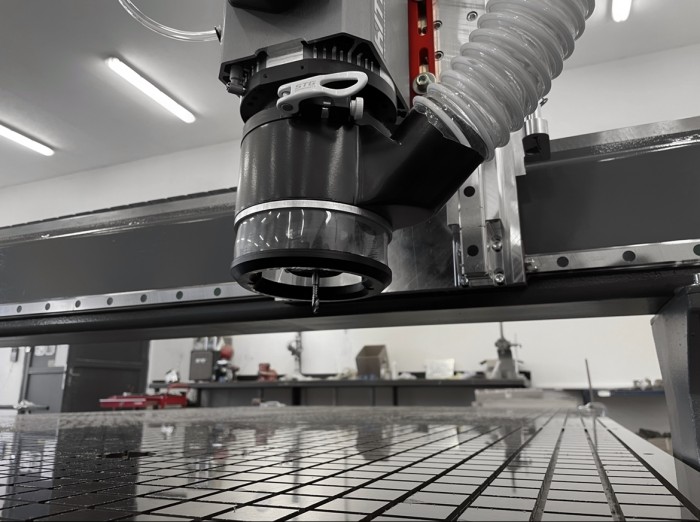
This device press on the material around cutting tool to provide high-quality processing of uneven and flexible materials. It is recommended for the processing of warped or curved sheets of a rigid material (for example, aluminum) and for the processing of thin and soft materials. This device can be also used to remove chips and dust during cutting.